When decorating, choosing a suitable ceiling material can greatly enhance the overall appearance and practicality of the space. Aluminum buckle plates have become a favorite among many households and commercial places due to their excellent moisture resistance, fire resistance, durability, and easy processing, meeting a variety of color and styling choices.
But you know what? The production process of aluminum buckle plate has many tricks. Today, let's talk about the three processes of roller coating, spray coating, and film coating, and see who is the best choice!
1. Roll Coated Aluminum Buckle Plate
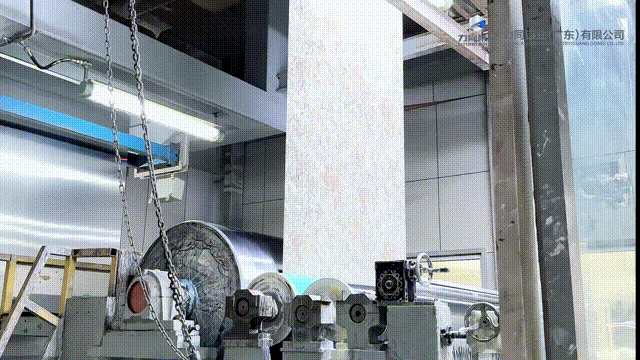
Appearance:
The substrate of roll coated aluminum buckle plate is roll coated color coated aluminum coil. Since the entire roll of aluminum coil is first color coated and then cut and processed, the resulting aluminum buckle plate has consistent color and minimal color difference; The overall surface is delicate and smooth, presenting a high-end texture; Whether it's fresh and elegant solid colors or realistic and natural 3D synchronized wood/stone patterns, they can perfectly restore color and texture details.
Performance:
The roller coating process endows aluminum buckle plates with excellent physical properties. The aluminum buckle plate processed by the three roll two coating process has high strength and can withstand a certain degree of impact and compression without deformation. Its surface coating is wear-resistant and scratch resistant. In daily use, even slight friction can maintain the integrity of the coating, and the surface of the board can maintain a beautiful appearance for a long time.
Durability:
Roller coated aluminum buckle plate has excellent durability, with its surface coating tightly attached to the aluminum plate, effectively resisting erosion from moisture, oil fumes, chemicals, and other substances. Daily cleaning is also very easy, just wipe gently with a damp cloth to remove surface stains and keep the ceiling clean and tidy.
2. Spray Painted Aluminum Buckle Plate
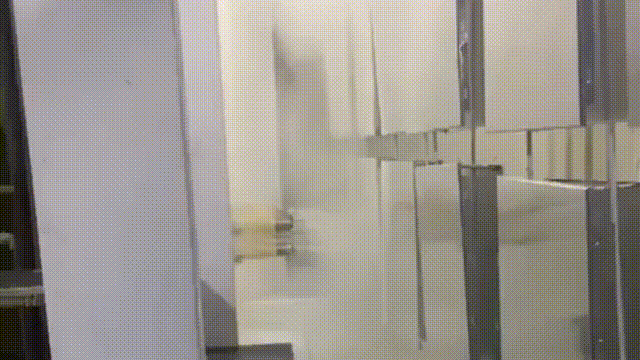
Appearance:
The spraying process is to spray color powder onto the surface of the stamped aluminum buckle plate through a spray gun. However, this method is prone to uneven color distribution. Upon careful observation, there may be a grainy texture on the surface of the aluminum buckle plate, and the color transition may not be natural enough. Especially when used on a large scale, the color difference between different plates is more obvious, which affects the overall aesthetics.
Performance:
The coating strength of sprayed aluminum buckle plate is relatively weak, and the adhesion of the coating is limited. After frequent friction or contact with sharp objects, the coating is easy to peel off, which affects the anti-corrosion performance of the aluminum plate and shortens its service life. In terms of weather resistance, sprayed aluminum buckle plates are slightly inferior. Prolonged exposure to natural environments such as sunlight and rain can easily cause color fading and powdering.
Durability:
Spray painted aluminum buckle plates have relatively low durability due to poor coating adhesion, easy fading, and other issues. Generally, after 5-10 years of use, obvious signs of aging may appear and require re spraying or replacement. In terms of maintenance, due to the granular texture of the sprayed aluminum buckle plate surface, it is prone to dust accumulation and difficult to clean after stains adhere, which increases maintenance costs and difficulty.
3.Iaminated Aluminum Buckle Plates
Appearance:
Film coating is the process of attaching a patterned or colored film onto the surface of an aluminum plate. Its color selection is rich and diverse, with a wide variety of patterns and good sensory effects. However, compared to roller coated aluminum buckle plates, the texture of the coated film is often slightly stiff and lacks a three-dimensional sense.
Performance:
The strength of laminated aluminum buckle plate is not much different from that of sprayed aluminum buckle plate. The laminated layer also has the problem of easy detachment. Moreover, once the film surface is scratched, the aluminum plate will be directly exposed, losing protection and easily rusting and corroding. In addition, the fire resistance of laminated aluminum buckle plates is relatively poor. In high temperature environments, the film may melt or even burn, posing certain safety hazards.
Durability:
The durability of laminated aluminum buckle plates mainly depends on the quality of the film. Ordinary laminated aluminum buckle plates may experience problems such as aging of the film surface and glue peeling after 3-8 years of use. Once these situations occur, it not only affects the appearance, but may also lead to damage to the aluminum plate. Moreover, when cleaning the laminated aluminum buckle plate, rough cleaning tools should not be used, otherwise it is easy to scratch the film surface, and extra care should be taken during maintenance.
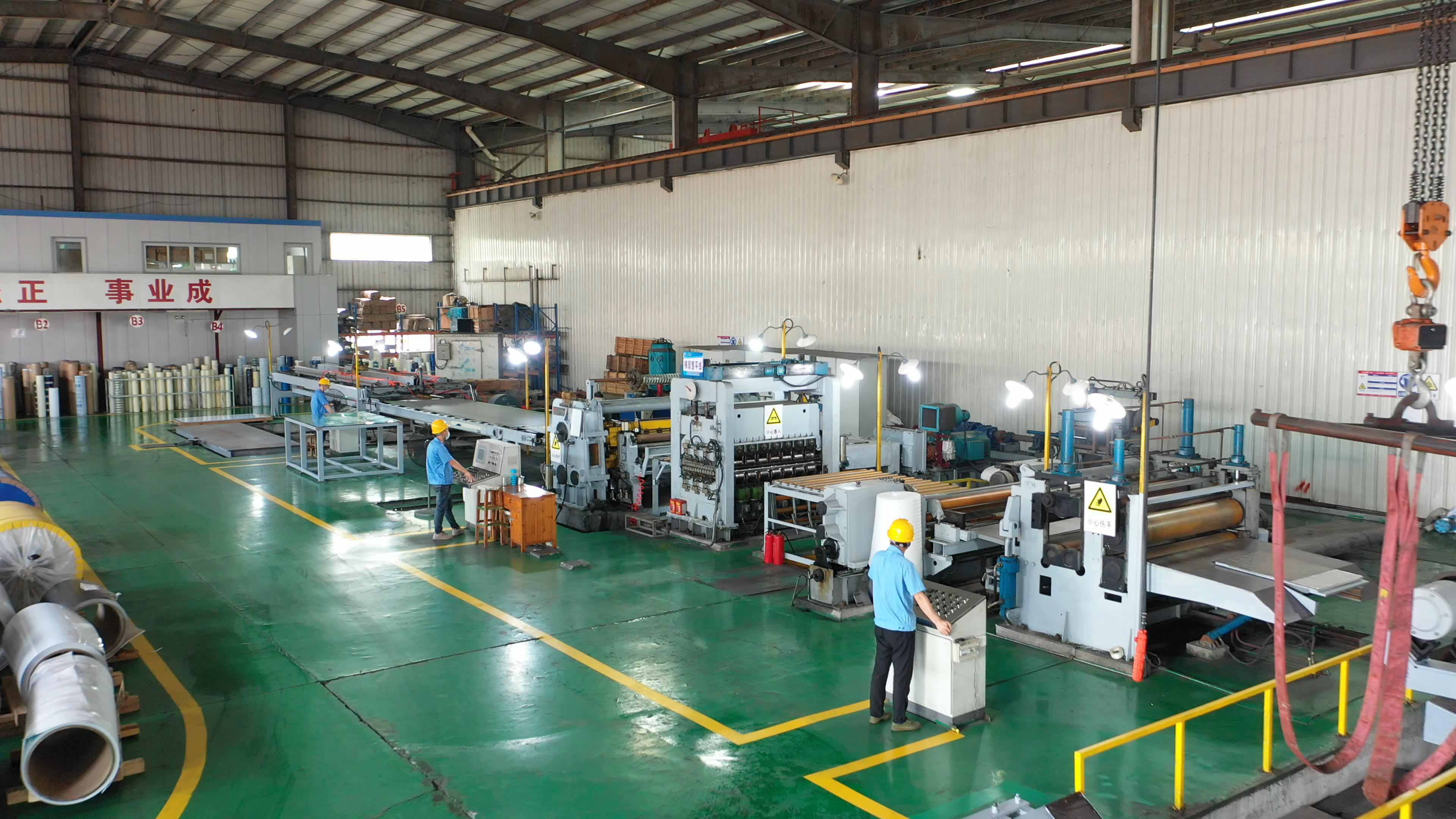
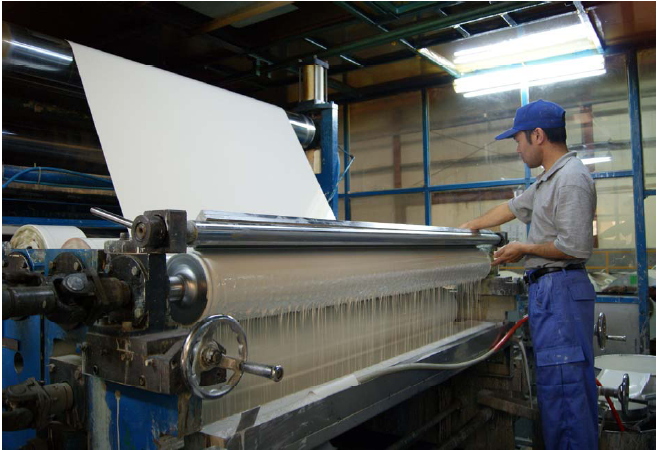
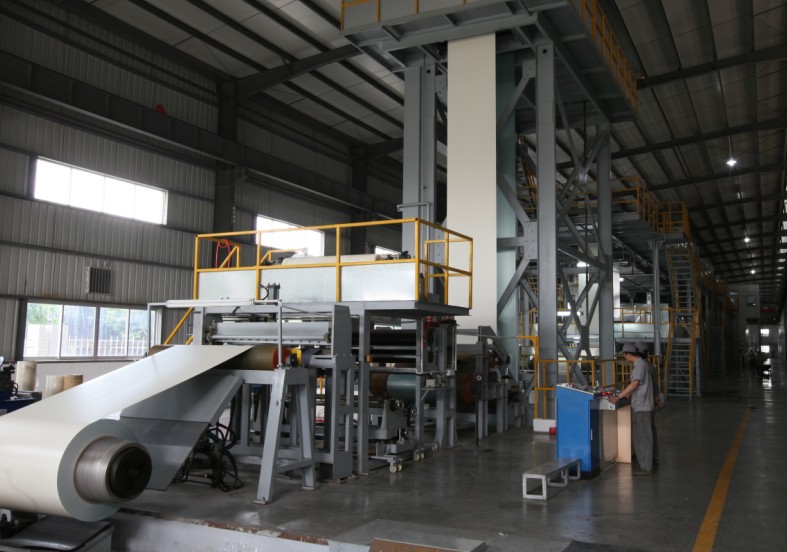
Litong Aluminum Industry, as an industry leader with over 20 years of experience in producing color coated aluminum coils, provides high-quality roll coated color coated aluminum coils for the production of aluminum buckle plates, helping to create better, more beautiful, and durable ceiling spaces.
If you are choosing aluminum buckle plates for decoration, you may consider aluminum buckle plates made of color coated aluminum coils produced by Litong Aluminum Industry Roll Coating, which can make your home or commercial space ceiling in one step and last as new for a long time!